Mittlerweile bin ich seit ca. 2,5 Jahren an dem Projekt dran, und es hat sich doch ziemlich weit in die gewünschte Richtung vom Bulldog weg entwickelt. Daher gönne ich dem Thema hier ein eigenen Baubericht und werde im Bulldog-Thread (den ich einen tollen Austausch zu dem Thema finde) einen Querverweis darauf machen. Der Bericht enthält auch allgemeine Überlegungen zur Gestaltung von Rockracern und zum Bau von Käfigelementen ohne Schweißen und Hartlöten.
Wie gestern im "Bastel-Thread" gezeigt: Das ist das, wo ich momentan stehe mit dem Fahrzeug. Den "Look" würde ich als weitgehend abgeschlossen bezeichnen, technisch wird noch das eine oder andere mit der Zeit dazu kommen.
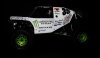

Vorüberlegungen
Als ich 2018 meinen Dune Fighter bei Conrad holten, hatte ich auch den Bulldog schon in der Hand. Die Entscheidung ist dann so 75% pro Dune Fighter, 25% pro Bulldog ausgegangen. Warum, kann ich heute nicht mehr wirklich sagen. Der Dune Fighter hat Spass gemacht, hat auch einen tollen "Look", aber immer wieder durch die zu schwach dimensionierten Diffs genervt. Mein Interesse an robusten Rockracern nahm recht schnell zu. Den Twinhammers gab es schon nicht mehr, als diese Überlegungen anfingen.
Eine zeit lang fand ich den GMade GOM sehr interessant: Für mich tolle Optik, Schaltgetriebe, anscheinend sehr guter Crawler. Ich habe viele Videos dazu gesehen, und der Finger war schon mehrmals auf dem Bestell-Button. Aber irgendwie war mir klar, dass das hochbeinige Teil "schnell" nicht wirklich gut kann und auch ziemlich "zugebaut" ist.
Den Yeti fand ich von Fahrvideos her einfach nur klasse. So sollte mein Rockracer "schnell" können. Die Karo gefällt mir aber überhaupt nicht. Sieht für mich aus, wie eine gechoppte asiatische Mittelklasselimosine auf einem (tollen) Offroad-Chassis. Das Gleiche gilt für mich übrigens auch für die Bulldog-Karo. Keine Ahnung, wo die Designer dafür meinen, Vorbilder gesehen zu haben. Auch der Rock Rey haut mich optisch jetzt nicht um. Ab dem Zeitpunkt war mir klar, dass ich mittefristig was mit einem halbwegs vorbildgetreuen "King-of-the-Hammers"-Look haben will, was ich dann wohl irgendwie selbst bauen muss, weil man es nicht kaufen kann. Ja, mittlerweile gibt es Lasernut und Hammer Rey. Tolle Fahrzeuge, finde ich, aber die gab es zu Beginn meiner Überlegungen noch nicht.
Gut, also Äußeres, d.h. eine realitätsnahe Silhouette, selbst gestalten. Zum Schweißen habe ich weder Talent noch Equipment. Ich hatte dann Ideen, was aus 6mm-Al-Rohr, mit Carbonstab gefüllt, mit diversen Klemm- und Schraubverbindungen zu machen. Anfangs war ich da bei einem mit dem Chassis fest verbundenen hinteren Käfig und einem abnehmbaren vorderen Teil. Wie schwer und haltbar das Ganze geworden wäre, keine Ahnung - es ist anderes gekommen.
Auch beim Yeti war die Maus schon mal auf "Bestellen", um ein gutes Basisfahrzeug für dieses Projekt zu haben. Schlussendlich stand aber leider schon "discontiued" beim Yeti auf der Axial-Homepage. Echt schade und für mich nicht nachvollziehbar, dass so ein tolles Fahrzeug eingestellt wird. Aber das wollte ich mir dann doch nicht geben, einen Haufen Geld und Arbeit in ein "Ersatzteil-Sorgenkind" zu stecken. So gingen die Überlegungen wieder auf den sehr günstigen Bulldog.
So, ich muss jetzt erstmal Schluss machen für heute. Mal noch 2 Skizzen, wo ich versucht habe, aus Bildern von den angestrebten Vorbildern Maße und Größenverhältnisse abzuleiten und das halbwegs auf das Bulldog-Chassis zu übertragen. Ausgegangen bin ich von den 40"-Rädern mit mutmaßlich ca. 1m Durchmesser.

Wie gestern im "Bastel-Thread" gezeigt: Das ist das, wo ich momentan stehe mit dem Fahrzeug. Den "Look" würde ich als weitgehend abgeschlossen bezeichnen, technisch wird noch das eine oder andere mit der Zeit dazu kommen.
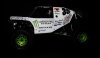

Vorüberlegungen
Als ich 2018 meinen Dune Fighter bei Conrad holten, hatte ich auch den Bulldog schon in der Hand. Die Entscheidung ist dann so 75% pro Dune Fighter, 25% pro Bulldog ausgegangen. Warum, kann ich heute nicht mehr wirklich sagen. Der Dune Fighter hat Spass gemacht, hat auch einen tollen "Look", aber immer wieder durch die zu schwach dimensionierten Diffs genervt. Mein Interesse an robusten Rockracern nahm recht schnell zu. Den Twinhammers gab es schon nicht mehr, als diese Überlegungen anfingen.
Eine zeit lang fand ich den GMade GOM sehr interessant: Für mich tolle Optik, Schaltgetriebe, anscheinend sehr guter Crawler. Ich habe viele Videos dazu gesehen, und der Finger war schon mehrmals auf dem Bestell-Button. Aber irgendwie war mir klar, dass das hochbeinige Teil "schnell" nicht wirklich gut kann und auch ziemlich "zugebaut" ist.
Den Yeti fand ich von Fahrvideos her einfach nur klasse. So sollte mein Rockracer "schnell" können. Die Karo gefällt mir aber überhaupt nicht. Sieht für mich aus, wie eine gechoppte asiatische Mittelklasselimosine auf einem (tollen) Offroad-Chassis. Das Gleiche gilt für mich übrigens auch für die Bulldog-Karo. Keine Ahnung, wo die Designer dafür meinen, Vorbilder gesehen zu haben. Auch der Rock Rey haut mich optisch jetzt nicht um. Ab dem Zeitpunkt war mir klar, dass ich mittefristig was mit einem halbwegs vorbildgetreuen "King-of-the-Hammers"-Look haben will, was ich dann wohl irgendwie selbst bauen muss, weil man es nicht kaufen kann. Ja, mittlerweile gibt es Lasernut und Hammer Rey. Tolle Fahrzeuge, finde ich, aber die gab es zu Beginn meiner Überlegungen noch nicht.
Gut, also Äußeres, d.h. eine realitätsnahe Silhouette, selbst gestalten. Zum Schweißen habe ich weder Talent noch Equipment. Ich hatte dann Ideen, was aus 6mm-Al-Rohr, mit Carbonstab gefüllt, mit diversen Klemm- und Schraubverbindungen zu machen. Anfangs war ich da bei einem mit dem Chassis fest verbundenen hinteren Käfig und einem abnehmbaren vorderen Teil. Wie schwer und haltbar das Ganze geworden wäre, keine Ahnung - es ist anderes gekommen.
Auch beim Yeti war die Maus schon mal auf "Bestellen", um ein gutes Basisfahrzeug für dieses Projekt zu haben. Schlussendlich stand aber leider schon "discontiued" beim Yeti auf der Axial-Homepage. Echt schade und für mich nicht nachvollziehbar, dass so ein tolles Fahrzeug eingestellt wird. Aber das wollte ich mir dann doch nicht geben, einen Haufen Geld und Arbeit in ein "Ersatzteil-Sorgenkind" zu stecken. So gingen die Überlegungen wieder auf den sehr günstigen Bulldog.
So, ich muss jetzt erstmal Schluss machen für heute. Mal noch 2 Skizzen, wo ich versucht habe, aus Bildern von den angestrebten Vorbildern Maße und Größenverhältnisse abzuleiten und das halbwegs auf das Bulldog-Chassis zu übertragen. Ausgegangen bin ich von den 40"-Rädern mit mutmaßlich ca. 1m Durchmesser.

Zuletzt bearbeitet: